Condition Based Maintenance in Power Generation Plants
INTRODUCTION
The power industry is experiencing an era of rapid transformation. New issues, such as the rapid adoption of renewable energy sources, deregulation, and a new emphasis on extending facility lifecycles, are forcing electric utility operators to carefully consider how they expend their resources and optimize their operations.
To sustain an efficiently operating unit and avoid failure of critical equipment, it is necessary to maintain the essential parts of that equipment. The effect of planned maintenance depends upon the methods used for preventative maintenance. It is required to apply corrective preventative techniques for critical equipment. The approach to preventive maintenance may become incompetent because it is tedious, costly, and may be harmful. So, it is necessary to determine the correct way depending upon the condition of Critical Equipment. It is required to correct the fault each time by applying a predictive maintenance strategy. Continuous feedback is compulsory for
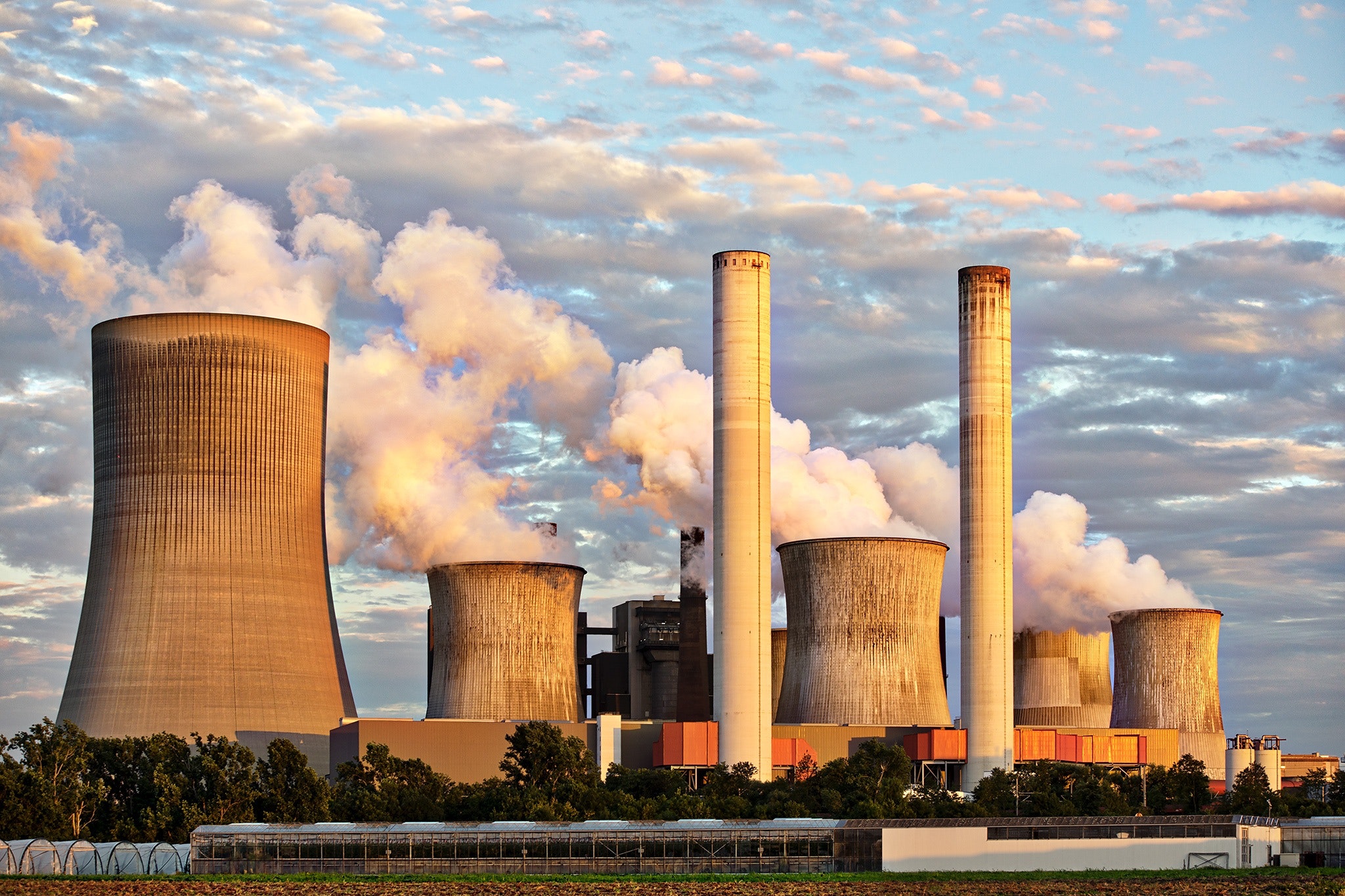
corrective preventive maintenance of Critical Equipment. It can be performed only by measurement of Critical Equipment performance.[rml_read_more]
Nowadays, operators are adopting condition-based maintenance and other proactive strategies that are driven by determining the actual condition of an asset rather than planned time-based scheduled maintenance. It eliminates unnecessary maintenance, minimizes unexpected failures, maximizes the use of resources and allows electric utility operators to increase reliability and availability. Condition-based monitoring can play a critical role in ensuring overall fleet availability, reducing the cost of downtime, and meeting regulatory requirements. It can help electric utilities avoid going off-line and reduce the risk of a forced derating or fines for dispatch schedule deviations by tracking asset health in real-time and avoiding unexpected equipment failures. It can also help utilities avoid losing real-time revenue streams and minimize the costly practice of buying replacement power from competitors.
CHALLENGES TO ELECTRIC UTILITIES
It has been predicted by the experts that the energy sector will experience many more changes in the decades to come than in the past hundred years. Alternative sources of energy, smart grids, and environmental concerns govern industry headlines. While asset health and maintenance do not attract the public’s attention, but many fleet managers now realize that new maintenance strategies can play a crucial role in making utilities more quick, cost-efficient, reliable, and, ultimately, more profitable.
The following trends will explain how new maintenance strategies not only lower maintenance expenses, but also extend to higher reliability, asset availability, and effectiveness. Innovative approaches to asset maintenance can help plan capacity, develop market strategies, link to workflow management, and reduce utility costs by allowing plant operators to connect real-time data on asset conditions with other operational data.
- Market Deregulation: Utilities functioning in deregulated markets subject to competitive pricing must pay hefty compensation for asset failure. Their primary concern is about ensuring the availability of plant resources at all times so they can maximize profits from open market sales and avoid expensive energy purchases to meet contract obligations. This critical need for high availability demands new approaches to tracking asset health and maintenance.
- Sustainable Energy: Increasing global interest in renewable energy and resulting electricity production is forcing many electric utilities to add alternative energy sources such as solar, wind, and geothermal to their fleets. The performance of sustainable power sources is weather dependent, and operators must maintain a diverse combination of power sources across their fleet to meet demand. To perform this complex task reliably, plant operators must continuously be aware of the condition and availability of their assets.
- Extending Plant Life: Building new power plants is expensive, and in this era of rapid technology change, electric utility owners may be hesitant to add more capacity to their fleet. Proactive maintenance strategies, by extending plant life can provide electric utilities more time to think about other options. It can be done only by the use of real-time condition monitoring instead of engineering calculations alone. Most regulations governing life extension applications (most notably in nuclear) require the use of real-time condition monitoring.
CHANGING TRENDS AFFECTS MAINTENANCE
Driven by the above trends, fleet managers are shifting their maintenance practices:
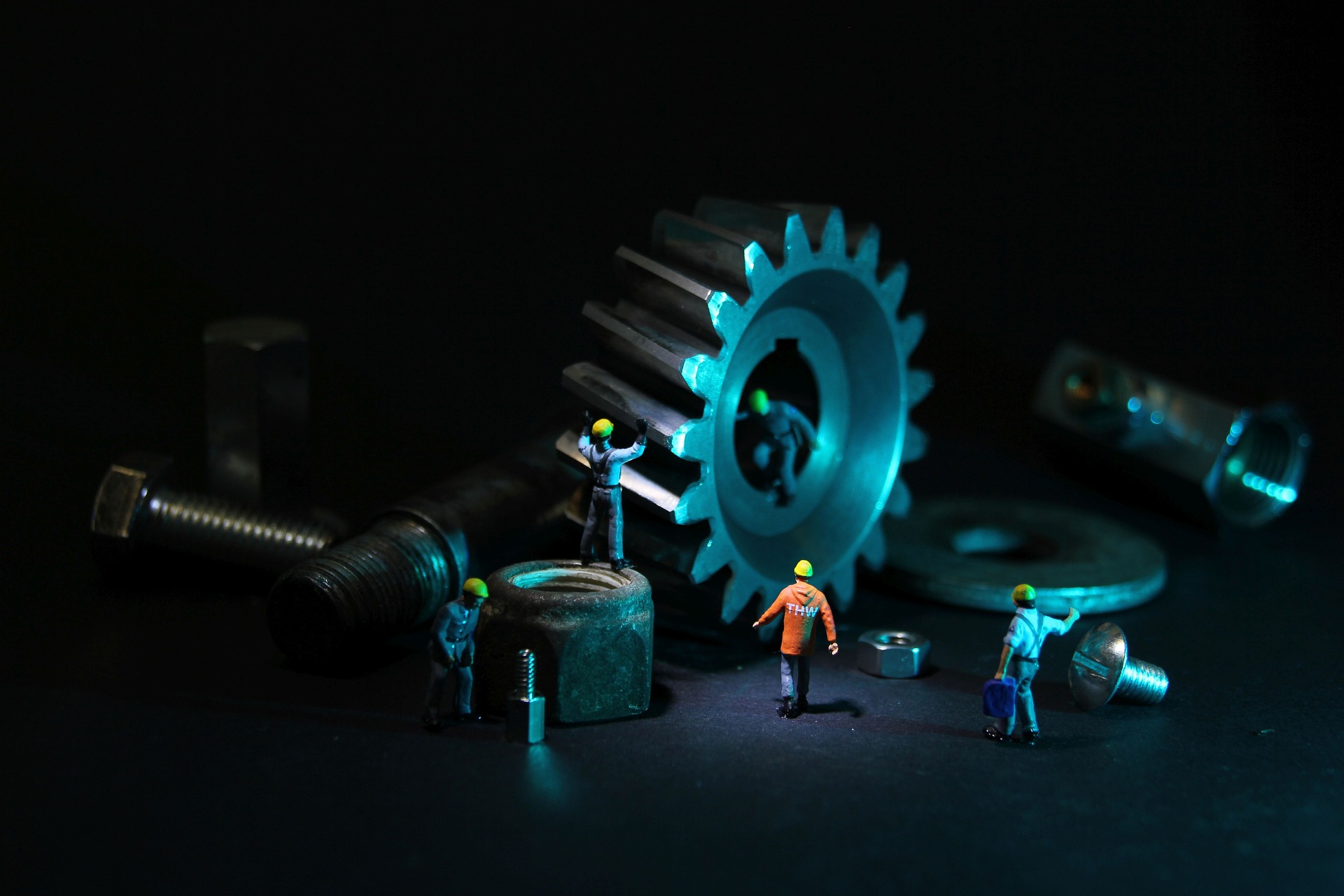
- They are now shifting from preventive and reactive maintenance to proactive and predictive maintenance based on real-time conditions.
- Moving from static, periodic equipment condition assessments to dynamic real-time online asset health monitoring.
- Developing data-driven predictive asset information to push leading indicators further back in time, giving plant operators more time to plan, increase uptime and reduce spare parts inventory.
- Developing monitoring, analytics, and maintenance systems that take advantage of subject manager experts, consultants, and original equipment manufacturers both inside and outside the company who specialize in maintaining specific types of assets such as turbines, pumps, heaters, or condensers.
- They are combining a range of diverse data sets into a single system for all plant and enterprise information to provide solutions for plant productivity and asset health.
- Implementing new infrastructure supporting maintenance requirements, such as less expensive wireless sensors, replacing tedious and inefficient manual data collection techniques.
CONDITION BASED MONITORING IS MORE EFFECTIVE MAINTENANCE
Power and utility industries today use diverse maintenance strategy spending over half its maintenance budget on highly expensive reactive maintenance strategies where maintenance only occurs after a piece of equipment fails. Alternative proactive maintenance strategies include strategies that use model-based learning systems to estimate asset lifecycles more accurately and give operators more time to plan capital expenditures and maximize availability. Proactive maintenance strategies use corrective, preventive and predictive processes to complement one another. Industry studies indicate that an average plant spends about more than 55% of its maintenance budget on reactive maintenance, which is the highest cost, while the top tier industry plants which utilize predictive technologies and proactive practices end up spending less than 10% of their budget on reactive strategies. Condition-based monitoring aka CBM is generally defined as a predictive maintenance technique that involves maintenance based on the actual state of a system. It is based on monitoring the underlying deterioration process of the equipment. As this deterioration reaches a predefined threshold level, a maintenance action is initiated. By predicting the Remaining Useful Life of a unit using remote monitoring techniques, operational and technical maintenance costs can be reduced.
CBM IMPLEMENTATION FRAMEWORK
The framework consists of essential building blocks that help to structure the implementation process. It offers prescriptive guidance within the process of unit selection, gives insights into the requirements of the condition indicator, and provides help within the prognostic model selection for the use in a CBM maintenance program. Finally, based on the Remaining Useful Life, insights in terms of the Total Relevant Maintenance Costs are obtained. Based on these insights, the potential of a CBM program for a specific unit can be evaluated.
A CBM program starts with monitoring asset parameters, then evaluates parameters with respect to limits, trends, and other asset data.
Eventually, it combines real-time data to comprehensive work management solutions.
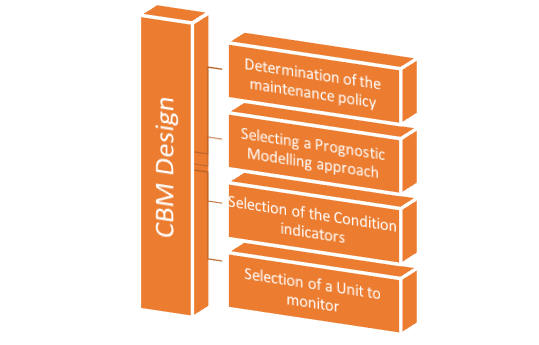
ADVANTAGES OF CBM OVER TRADITIONAL SYSTEMS:
- Reduced capital costs
- Extended asset lifecycles
- Reduced maintenance costs because equipment that is operating well is not repaired or replaced
- Better asset reliability
- Improved asset availability
- Improved asset utilization including longer lifecycles and better-informed capital expenditures
- Minimized lost production time by better predicting asset failures
- Optimized maintenance intervals
THE APPROACH FOR CONDITION-BASED MAINTENANCE:
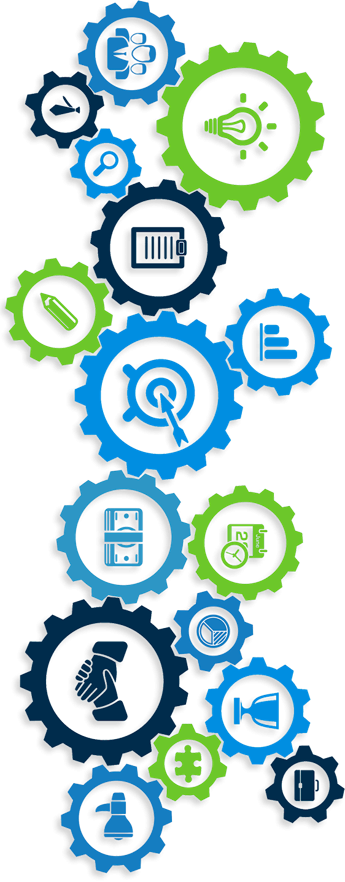
- Reach Your Assets:Specific maintenance strategies are better for certain assets than others. The optimal maintenance strategy is dependent upon several factors, including the cost of failure, the return on investment, and the full lifecycle cost of the asset.
- Collect Already Available Data:Many organizations have a precious asset health-related data with the potential to provide tremendous insight into the status of their assets.
- Add New Data Through Sensors:As operators consider the best approach to deploying sensors, they should be guided by the experience of others who have already traveled that road.
- Combine all the Data:With the appropriate sensors in place, combine all the data in an electronic database for consolidation, processing, and utilization to create a complete and clear image of maintenance requirements.
- Analyze the Data:Transportation organizations should understand that their CBM applications are not a “set-it-and-forget-it” proposition. The algorithms are moving targets that need regular updates to incorporate the most current asset experience.
OBSTACLES TO CBM IMPLEMENTATION
Power companies implementing CBM face several challenges. Technologically the CBM system must ensure that each stakeholder has access to the data so that they can make effective decisions. At the enterprise level, this typically requires the collection of data from disparate systems. Data must be consistently formatted, displayed, viewed, analyzed, and correlated. Data collected in real-time must be time-stamped in a uniform manner to correctly attribute it to specific events. At last, users must be able to simply and easily access and share data across the organization. Aligning asset hierarchies to data points and building effective and accessible data visualization strategies are also critical to the success of any CBM system.
Management should have faith across the organization in the new systems before the transition begins. Typically, a CBM program affects a wide range of assets. Usually, there is no single solution for one asset type. The prospect of making such a wholesale transition can seem overwhelming to many personnel. One-way managers can overcome this concern is by starting a CBM implementation with just a few critical assets. CBM implementation should consider the following up-front costs and potential liabilities:
- Cost training staffs
- Monitoring & instrumentation costs of equipment
- Modifications to retrofitting older assets with sensors
- Fatigue or uniform wear failures
- Unpredictable maintenance intervals
COMPONENTS OF ARNOWA’S CBM SYSTEM
Data Collection
Sensors and smart meters deployed collects data from disparate data sources. Arnowa supports more than 400 standard interfaces.
Storing, Managing and Enhancing Data
Arnowa’s gateway locally filters, stores, and send high-quality data to the cloud for cloud computing. This helps engineers and business users find, analyze and report data for faster decision making. It also leverages flexibility by allowing users to configure custom alerts based on any data source. With notifications, users can set the platform to send alerts whenever specified equipment exceeds pre-set parameters. This capability helps operators detect potential maintenance problems as early as possible.
Data Visualization and Delivery
Arnowa’s Dashboard, combined with Excel’s computational, graphics, and formatting capabilities, offers powerful tools for gathering, monitoring, analyzing, updating, and displaying real-time data and events. It allows users to gain insight into plant operations by creating interactive graphical displays. Users can create displays using either real-time or historical data collected in the system
By monitoring process behavior, users can compare current data with past events to quickly identify issues and remedy problems. Users can efficiently perform analysis, discover answers, share displays, and insights with other users, encouraging collaboration across the enterprise.
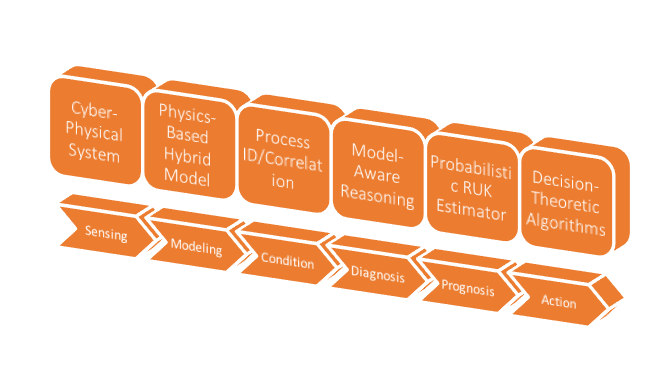
How does Arnowa’s CBM system work?
- Sensing that’s robust enough to yield accurate system data.
- Modeling that is customized and which can simulate adverse conditions and failures the system is designed to prevent.
- Condition Monitoring that reliably monitors anomalies from expected system behavior.
- Diagnostics that contain efficient reasoning engines which isolate and infer root causes of faults within sub-systems.
- Prognostics that use system models and data to probabilistically predict a system’s useful life span.
- Actionable Recommendations based on decision-theoretic algorithms to promote accurate planning.
ARNOWA’S OFFERINGS (HARDWARE & SOFTWARE)
- Sensors: Sensors for parameters such as temperature, vibration, humidity, noise, etc., provide essential information about the process or the entire plant. They either directly measure physical values or use existing measures to indirectly calculate additional information. This information is the enabler for the implementation of advanced automatic functions, process models, as well as condition monitoring.
- Wireless Data Transmission Devices (Nodes, Gateway, Edge): These devices store and transmit data to the cloud safely.
- Arnowa Application Software: It helps in the monitoring and visualization of data.
- Data Analytics Support (real intelligence): Our highly qualified and experienced intelligence team will convert the data received from the sensors in the usable form so that industries can use that data into their operational activities.
ABOUT ARNOWA
Arnowa is a smart real-time data acquisition, analytics, reporting, verification, and management system. Combined with artificial and real intelligence, Arnowa supports proactive monitoring, converting data to knowledge, predicting issues, periodic reporting, advising improvements, alarming, and making informed business decisions. It involves a human interface, which provides expert analysis of the information and knowledge stimulated out of the monitored data and converts it into wisdom that can be used for efficient decision making, improving the present as well as the future. Arnowa facilitates audit needs and improves management by providing transparency, accuracy, and useful advice.
Arnowa not only monitors and records data, but also provide a series of existing problems, diagnose the inefficient points, and provides a solution to maintain efficiency levels through timely reporting and continuous support.
We help our clients improve asset performance at their businesses by offering improved efficiency through proactive energy, water, and environment management. We enable you to keep track of your assets and get real-time insights from anywhere around the world. Our team of expert professionals will be guiding you with timely recommendations on efficiency improvements and supporting your business in times of need to make the right choices.
REFERENCES
[1] International Atomic Energy Agency (IAEA), 2017. Implementation Strategies and Tools for Condition Based Maintenance at Nuclear Power Plants. Link: https://www-pub.iaea.org/MTCD/publications/PDF/te_1551_web.pdf
[2] Nagar, T., 2006. CONDITION BASED MAINTENANCE POWER PLANT MACHINERIES THROUGH NON DESTRUCTIVE TESTING AND EMERGING TECHNIQUES.
[3] https://www.plant-maintenance.com/articles/CBMPowerPlants.pdf
[4] Joshi, M.M., Maintenance Method For Critical Equipment Of Coal Handling Plant. Link: http://www.total-productive-maintenance.com/articles/Critical_Equipment_Maintenance.pdf
[5] David Berger, 2006. Six steps to condition-based maintenance. Link: https://www.plantservices.com/articles/2006/199/
[6] Paul, S., 2018. Condition Based Maintenance Program for Combined Cycle Power Plant. Available at SSRN 3331440. Link: https://papers.ssrn.com/sol3/papers.cfm?abstract_id=3331440
[6] Fumeo, E., Oneto, L. and Anguita, D., 2015. Condition-based maintenance in railway transportation systems based on big data streaming analysis. Procedia Computer Science, 53, pp.437-446.